Polymer/Extrusion Melt Pump for Plastic Extrusion
Contents
Extruder Gear Pump
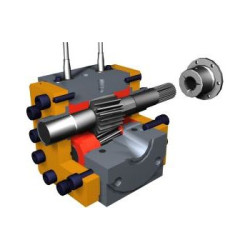
Melt Pump Applications
- Sheet and Film Extrusion (tape plant, woven sack plant, lamination and PP plants, box stapping plant, mono filaments, non-woven fabrics)
- Compounding (master batch)
- Pipe/Profile/Cable Extrusion
- Rubber Extrusion
Technical Specifications
- Materials: PET, PS, PP, PE-LLD, PE-HD
- Throughput: 30-12,000 kg/h [66-26,400 lb/h]
- Difference Pressure – standard (max.): 250 bar [3,626 psi]
- Difference Pressure – option (max.): 500 bar [7,252 psi]
- Viscosity: 5-20,000 Pas
- Temperature (max.): 350°C [662°F]
- Misc.: Full nitriding depth of gear teeth (unique among melt pump manufacturers)
- Melt Pump Manufacturer: Eprotec (made in Switzerland)
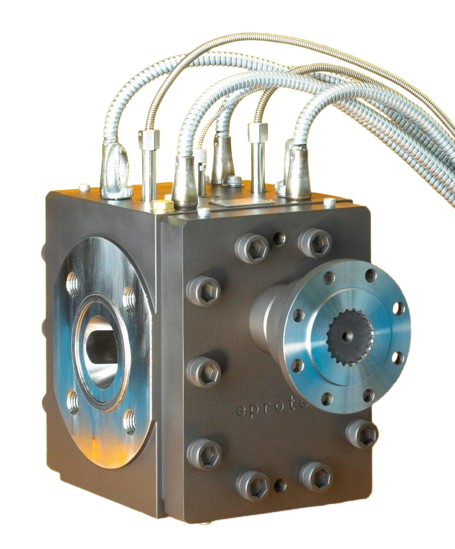
Output Melt-X Models (in kg/h):
Model | Flow Rate (ccm/rev.) | PE-HD pipe | PE-LD film | PP sheet | PS sheet | PET sheet |
melt-X1 | 25.5 | 105 | 140 | 160 | 200 | 220 |
melt-X2 | 45.2 | 180 | 240 | 260 | 320 | 350 |
melt-X4 | 90.0 | 300 | 400 | 480 | 570 | 600 |
melt-X7 | 175.9 | 500 | 700 | 850 | 1,100 | 1,200 |
melt-X10 | 364.0 | 830 | 1,300 | 1,500 | 1,900 | 2,100 |
melt-X20 | 706.0 | 1,400 | 2,200 | 2,400 | 3,100 | 3,400 |
melt-X40 | 1463.0 | 2,400 | 3,800 | 3,900 | 4,900 | 5,400 |
melt-X80 | 3140.0 | 6,300 | 7,500 | 8,000 | 10,000 | 12,000 |
Output Melt-X Models (lb/h):
Model | PE-HD pipe | PE-LD film | PP sheet | PS sheet | PET sheet |
melt-X1 | 231 | 308 | 352 | 440 | 484 |
melt-X2 | 396 | 528 | 572 | 704 | 770 |
melt-X4 | 660 | 880 | 1,056 | 1,254 | 1,320 |
melt-X7 | 1,000 | 1,540 | 1,870 | 2,420 | 2,640 |
melt-X10 | 1,826 | 2,860 | 3,300 | 4,180 | 4,620 |
melt-X20 | 3,080 | 4,840 | 5,280 | 6,820 | 7,480 |
melt-X40 | 5,280 | 8,360 | 8,580 | 10,780 | 11,880 |
melt-X80 | 13,860 | 16,500 | 17,600 | 22,000 | 26,400 |
Melt Pump – Special Options
Model | Application | Description | Examples |
melt-XS | Thermally critical materials | Lubrication flow and drainage is led outside: for optical/transparent and shear-sensitive and temperature-sensitive polymers | PC (polycarbonate), PMMA (polymethylmethacrylat), TPE-V, PE-X |
melt-XC | Thermally critical materials | Circulation loop for better temperature control: to reduce temperature increase of polymer | automotive TPO profiles |
melt-XMB | Low-viscosity materials | to process extremely low-viscosity materials (such as MFI 1500) | PP (polypropylene) in mask filter production |
melt-XH | High-pressure | For materials and applications that generate high pressure up to 500 bar [7,252 psi] | highly viscous polymers, elastomers, small micro granules, thin profiles and tubes |
melt-XR | Abrasive material with high filler content | to process material with high filler content, e.g. 83% CaCO3, 80% BaSO4 or 50% glass fiber | recycling and compounding |
ATEX EX II | ATEX environments | Temperature control with thermal fluid (oil) | ATEX environments |
Pump with Amorphous Surface | All applications | Amorphous surface prevents material build-up and allows faster color change | all applications |
Melt/Gear Pump Function in Plastic Extrusion
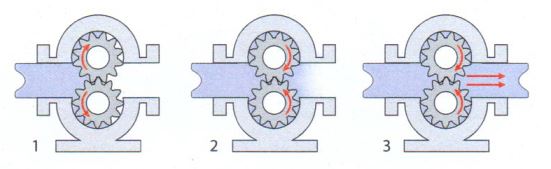
Fig.1: Two externally toothed gear wheels mate with each other when they rotate (counter-rotating non-intermeshing). A small pressure, generated by the extruder installed upstream, is sufficient to fill the tooth chambers (Fig. 1)
Fig 2: On the discharge side, the mating of the gear teeth in each other conveys the melt out of the tooth chambers.
Fig 3: The forces on each of the gear shafts are taken up by two slide bearings. These are lubricated by the plastic and are maintenance-free
Melt Pump Control
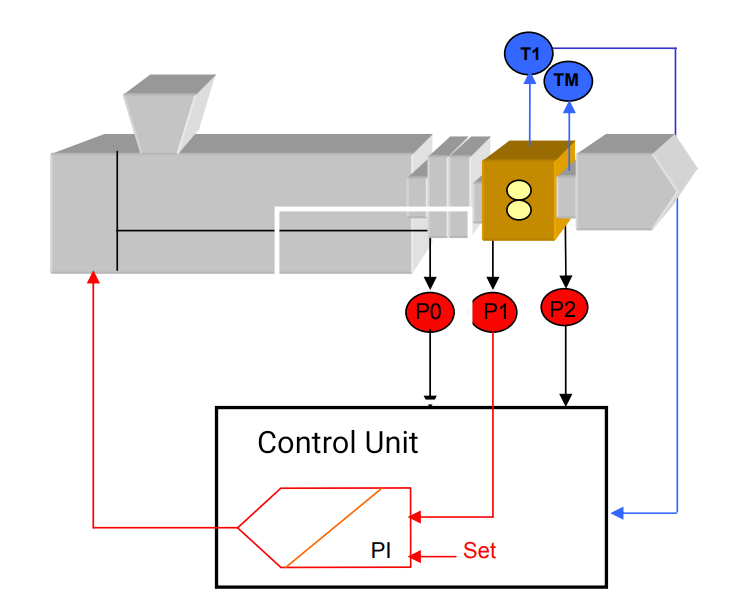
Melt Pressure Gauge and Control (P1)
Melt Pressure Gauge (P2)
Temperature Control Pump (T1)
Melt Temperature Sensor (TM)
There are different ways to synchronize the melt pump with the extruder. The control unit of the extruder may already have the option to implement an external device such as a melt pump. Or the melt pump is operated with a separate melt pump control unit which synchronizes extruder and melt pump (either via 0-24V DC or 0-10V DC control signal). Here the two most common melt pump control modes are the so-called ‘extrusion mode’ and ‘compounding mode’
- Extrusion Mode:
The pump inlet pressure (P1) is measured by a pressure gauge. The melt pump control compares the set pressure with the actual pressure and then regulates the extruder screw speed. - Compounding Mode:
The pump inlet pressure (P1) is measured by a pressure gauge. The melt pump control compares the set pressure with the actual pressure and then regulates the speed of the melt pump.
How to choose the right melt pump?
When choosing a melt pump for extrusion following criteria must be considered:
- Flow Rate (minimum, maximum, normal)
- Inlet and Discharge Pressures (minimum, maximum, normal)
- Application (e.g. Compounding, Sheet/Film extrusion, Rubber extrusion etc.)
- Type of Polymer & Viscosity (e.g. PP, PET, HDPE etc.)
- Temperature (minimum, maximum, normal)
- Filler Content (percentage and kind of filler/solids)